Hybrid racing is a team that builds a formula one style hybrid race car that competes against other student teams at the FSAE Hybrid competition at the New Hampshire motor speedway each year. In my 4 years on the team I have designed a spaceframe chassis in NX, conducted analysis in Ansys, designed a jigging system for our chassis, led welding of our space frame chassis, and led the vehicle dynamics and chassis division consisting of over 15 people with a $5000 budget.
MER-19
2018-2019
While designing a new spaceframe chassis for our electric racecar, I had to consider four constraints (listed in order of my priority): the rules, packaging, stiffness targets, and weight. What made this chassis different from our previous ones was the shift from an ICE engine with two accumulators in the sidepods to one rear mounted accumulator. I spent 4 months designing this chassis and used 1D beam analysis in NX Nastran simulation to calculate the stiffness. The final chassis met all of the required constraints, weighs 80 lbs, and has a torsional stiffness of 1400 NM/deg.
MHR-18
2017-2018
During the 2017-2018 season, I served as the Vehicle Dynamics and Chassis division (VDC) lead. I was responsible for ensuring the chassis, suspension, steering, corners, and pedalbox were designed, built, and tested in time for competition. This meant planning meetings, allocating budgets, designing and analyzing parts, managing manufacturing, and coordinating projects with other divisions.
As the division lead, I took a very different approach to leadership than my predecessors. The leads before me were very focused on only the car. They spent all their time designing and manufacturing on their own and spent very little time teaching new members and giving them projects. As such, our division was very small. Only 2 new members joined the division when I was a freshman and only 1 joined the year after. I identified this as a key problem and sought to fix this as a new leader. I used a transformational leadership approach to new members and made sure they all had projects to work on and knew how to accomplish them. Many times I had to make the choice whether to spend 1 hour doing a project my self or spend 3 hours teaching a freshman how to do it; I almost always chose the latter because having a division as small as ours was unsustainable for future years and new members are the lifeblood of our team. Thanks to my efforts, the VDC division became the largest on the team, having over 15 members which was significantly more than the 5 we had the prior year.
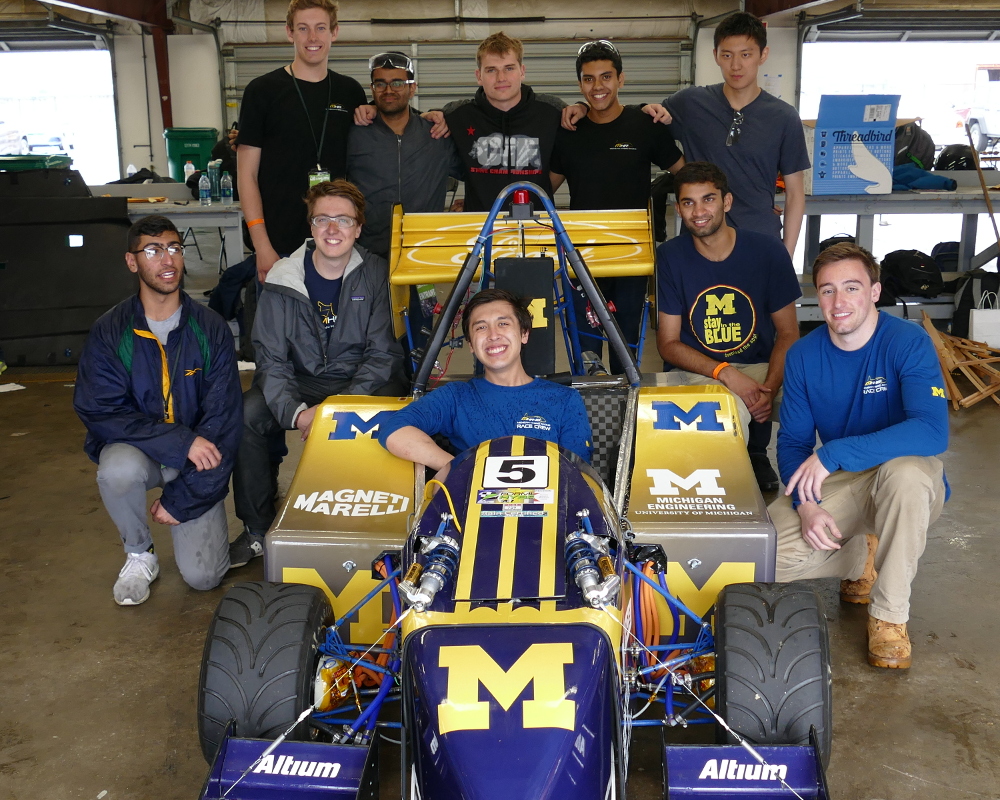
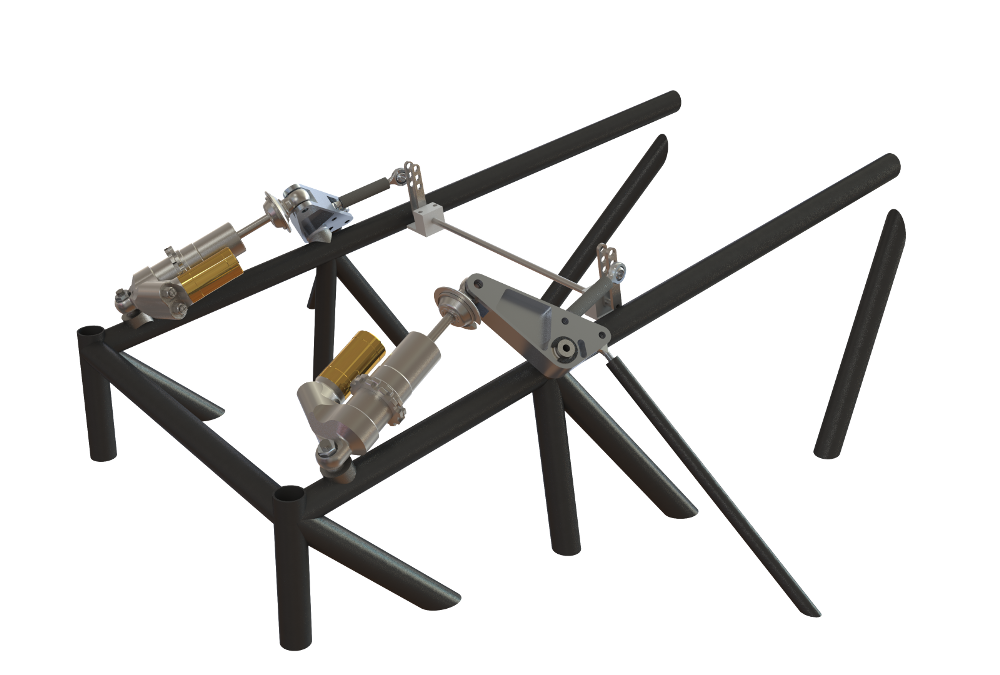
Along with my responsibilities to lead my division, I did a lot of design and analysis for the MHR-18 car myself. I helped our suspension lead with front suspension design by finding a location for our rocker and damper on the top of the car that would put our forces in plane. We switched from a bottom mounted pull-rod to a top mounted push-rod to make space for our in-hub electric motors. I also performed FEA analysis on many of our tabs and suspension rockers to ensure they would not yield under braking or cornering forces. For manufacturing, I did all of the welding on our chassis tabs and suspension control arms and milled grooves into our A-Arms to stake bearings.
As a leader I recognized that I not only had a commitment to my division, but to the entirety of the team. I led SolidWorks sessions to teach everyone on the team how to use the software at a basic level to help them with their CAD projects. I had 5 session teaching basic features like sketching as well as complex features like configurations. Additionally, I led and organized “chili cook-off” and “cookie bake-off” social events so new members could get to know the existing members on the team.
MHR-17
2016-2017
During the 2017-2018 season, I was the chassis manufacturing lead, meaning I was in charge of taking the chassis from a CAD model into a physical frame. In order to weld a spaceframe chassis, you need a jigging system to ensure that important parts of the chassis such as roll hoops and suspension components are located properly so the chassis does not warp during welding. I designed a jigging system in SolidWorks that would clamp the important tubes to a thick steel plate. I milled these jigs and TIG welded the entire chassis in 2 weeks. The project was completed on budget and on schedule.
MHR-16
2015-2016
I first joined the team as a freshman during the 2015-2016 season where I helped with design, milling, and welding. Unlike my peers who did FIRST in high school, I had no experience with engineering or metal machining so I had to learn it all as I went along. I initially helped with front and rear hub design and milled several chassis tubes. Once I got welding training and did enough practice on my own to get myself to a reasonable level, I started welding on our car. Despite having no previous background in welding, I pushed myself and spent dozens of hours practicing. I welded both of our side-pods on, welded a majority of a our tabs, and welded all of our spare suspension arms.